Understanding What is Porosity in Welding: Reasons and Solutions
Understanding What is Porosity in Welding: Reasons and Solutions
Blog Article
Porosity in Welding: Identifying Common Issues and Implementing Finest Practices for Prevention
Porosity in welding is a pervasive issue that often goes undetected till it triggers significant problems with the honesty of welds. This usual flaw can compromise the strength and durability of bonded structures, posing safety and security threats and resulting in costly rework. By recognizing the origin triggers of porosity and implementing reliable prevention strategies, welders can significantly boost the high quality and reliability of their welds. In this conversation, we will discover the crucial elements adding to porosity formation, analyze its damaging effects on weld performance, and review the most effective practices that can be embraced to minimize porosity event in welding processes.
Typical Causes of Porosity
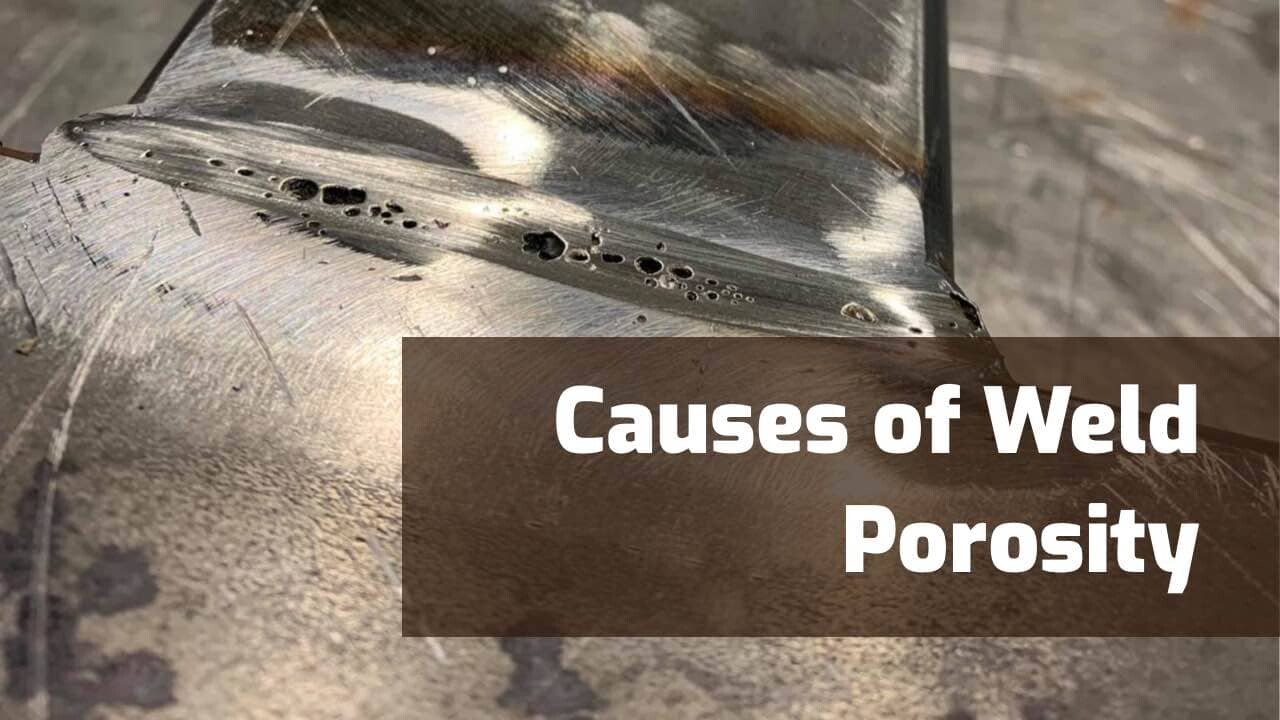
Utilizing filthy or wet filler products can introduce impurities right into the weld, adding to porosity issues. To reduce these common reasons of porosity, complete cleaning of base steels, appropriate shielding gas option, and adherence to ideal welding parameters are crucial methods in achieving high-quality, porosity-free welds.
Influence of Porosity on Weld High Quality

The presence of porosity in welding can dramatically jeopardize the architectural stability and mechanical residential properties of welded joints. Porosity produces voids within the weld steel, weakening its general strength and load-bearing capability. These gaps serve as stress concentration factors, making the weld more prone to cracking and failing under used loads. Furthermore, porosity can reduce the weld's resistance to rust and various other environmental elements, better decreasing its long life and performance.
Welds with high porosity degrees have a tendency to display lower impact strength and lowered capacity to flaw plastically prior to fracturing. Porosity can hamper the weld's capacity to effectively transmit forces, leading to early weld failing and potential safety and security dangers in critical structures.
Best Practices for Porosity Prevention
To great site improve the architectural integrity and high quality of welded joints, what details measures can be executed to lessen the event of porosity during the welding process? Utilizing the right welding strategy for the specific material being welded, such as adjusting the welding angle and gun setting, can better protect against porosity. Regular evaluation of welds and instant remediation of any type of problems recognized throughout the welding procedure are essential practices to prevent porosity and produce premium welds.
Value of Correct Welding Strategies
Applying correct welding strategies is extremely important in ensuring the structural integrity and quality of bonded joints, building on the structure of reliable porosity avoidance procedures. Welding methods directly impact the overall strength and resilience of the welded structure. One vital facet of correct welding methods is preserving the appropriate heat input. Excessive warmth can cause boosted porosity because of the entrapment of gases in the weld pool. Alternatively, not enough warm may lead to incomplete blend, developing you can try this out prospective powerlessness in the joint. In addition, utilizing the suitable welding parameters, such as voltage, existing, and take a trip speed, is crucial for attaining sound welds with minimal porosity.
In addition, the choice of welding procedure, whether it be MIG, TIG, or stick welding, must align with the details needs of the project to make certain optimal outcomes. Proper cleaning and prep work of the base metal, along with selecting the right filler product, are also crucial components of skillful welding techniques. By sticking to these ideal practices, welders can reduce the threat of porosity development and produce premium, structurally audio welds.
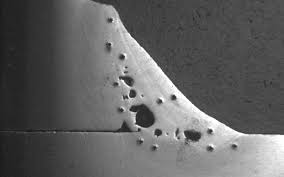
Examining and Quality Assurance Procedures
Quality assurance steps play a crucial role in confirming the honesty and reliability of welded joints. Evaluating treatments are essential to discover and stop porosity in welding, making certain the strength and sturdiness of the end product. Non-destructive screening methods such as ultrasonic testing, radiographic testing, and visual evaluation are frequently used to recognize possible issues like porosity. These techniques enable the assessment of weld quality without compromising the stability of the joint. What is Porosity.
Post-weld examinations, on the other hand, examine the last weld for any type of issues, including porosity, and verify that it fulfills specified requirements. Applying an extensive top quality control plan that includes complete testing procedures and assessments is paramount to decreasing porosity concerns and ensuring the overall high quality of bonded joints.
Verdict
To conclude, porosity in welding can be a typical problem that influences the quality of welds. By identifying the typical reasons of porosity and applying ideal practices for prevention, such as appropriate welding strategies and screening measures, welders can guarantee premium quality this article and trustworthy welds. It is vital to prioritize prevention methods to minimize the occurrence of porosity and maintain the stability of welded structures.
Report this page